CHEMICAL PRODUCTS
Use the keywords below to discover products that fit your exact mixing needs.

-
All
-
High Shear
-
In-tank
-
Dispersion
-
Diaf
-
Inline
-
Lab Mixers
-
Powder Induction
-
Low Shear
-
Accessories
-
Static
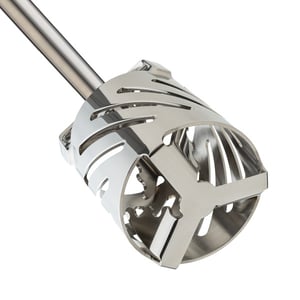
READ MORE
Rotosolver® CXThe Ultimate High Shear MixerREAD MORE
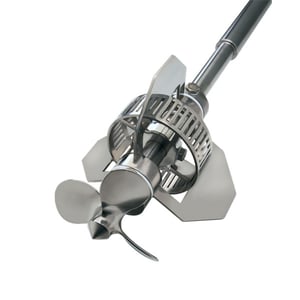
READ MORE
Rotostat® CXHigh Shear EmulsifierREAD MORE
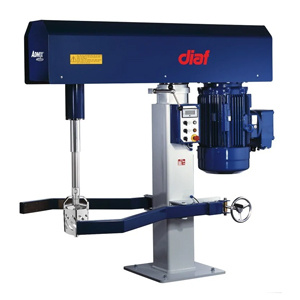
Read More
Diaf Dissolver CXHigh Speed, High Shear DisperserRead More
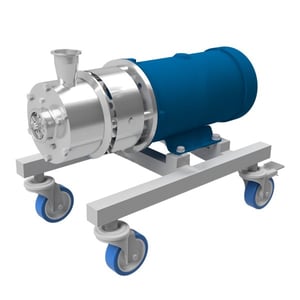
READ MORE
Dynashear® CXInline Continuous Mixer / EmulsifierREAD MORE

READ MORE
Benchmix® CXBenchtop Lab MixerREAD MORE
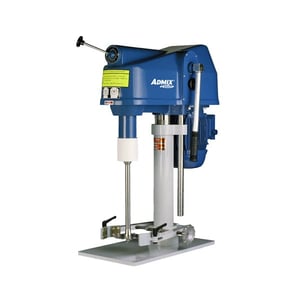
READ MORE
Diaf Minibatch™ CXVersatile Benchtop DisperserREAD MORE
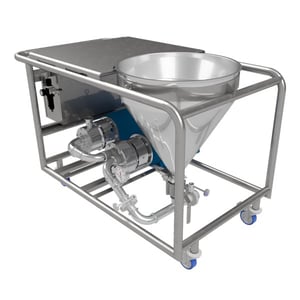
Read More
Fastfeed® CXPowder Feed & Dispersion SystemRead More
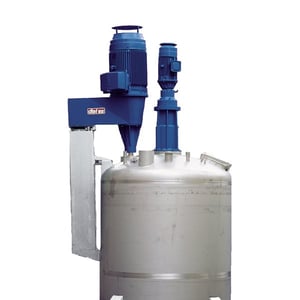
Read More
Diaf Diamix™ CXEnclosed System for DispersionRead More
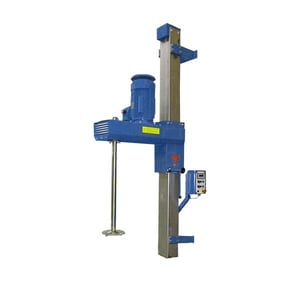
Read More
Diaf Diatint™ CXIndustrial Mixer for Mobile ContainersRead More
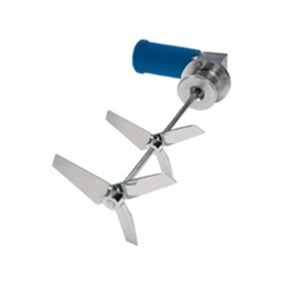
READ MORE
Rotomaxx™ CXHigh Torque MixerREAD MORE
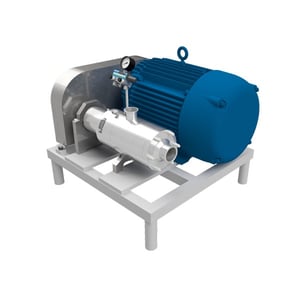
READ MORE
BSM™ CXHigh Intensity Rotor StatorREAD MORE
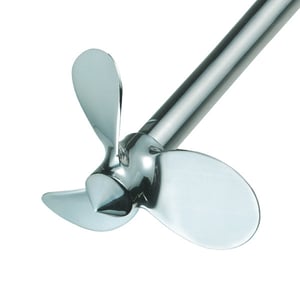
READ MORE
Rapidex™ CXLow Shear Propeller AgitatorREAD MORE
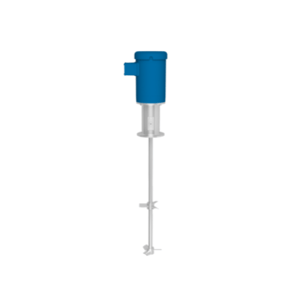
READ MORE
Rotomixx™ CXPortable Low Shear Batch MixerREAD MORE
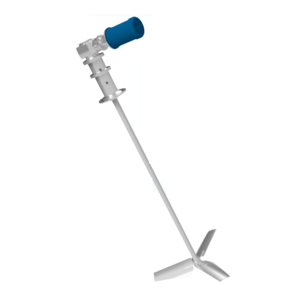
READ MORE
Rotomaxx™ II CXLow Speed, Large Capacity AgitatorREAD MORE
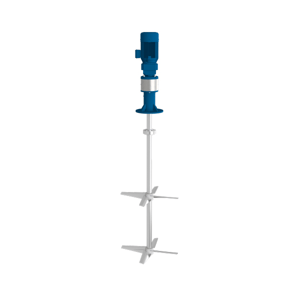
READ MORE
Rotomaxx™ III CXHigh Efficiency, Slow Speed AgitatorREAD MORE
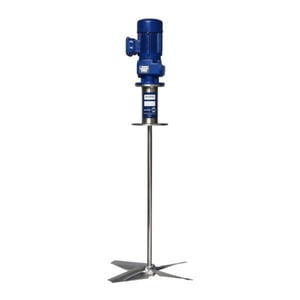
READ MORE
Rotofoil® CXLow Shear AgitatorREAD MORE
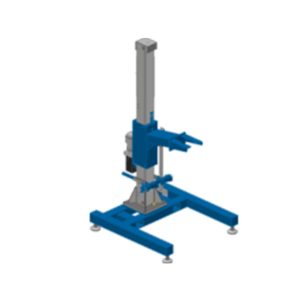
READ MORE
Lift StandsMobile and Wall MountedREAD MORE
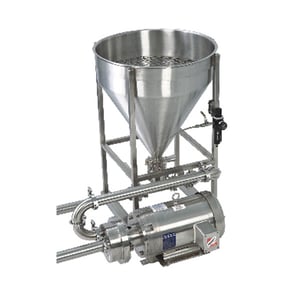
Read More
Optifeed™ CXAtmospheric Feed SystemRead More
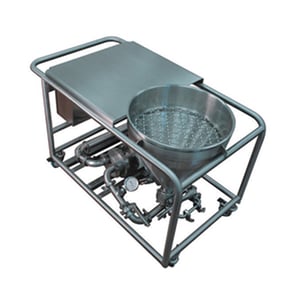
Read More
PIC™ CXAtmospheric Feed System with Work TableRead More
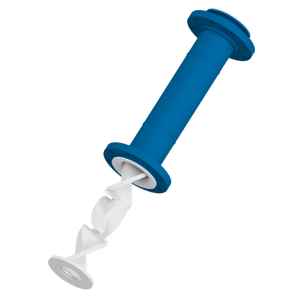
READ MORE
Admixer™ CXStatic Mixer and BlenderREAD MORE
SCHEDULE A MEETING WITH OUR LAB MANAGER
Chemical Customers
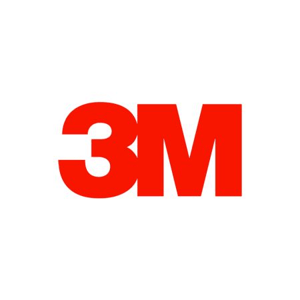
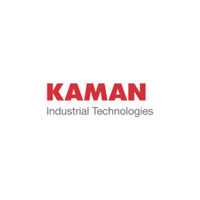
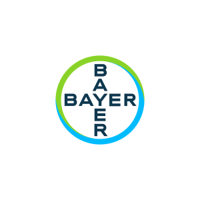
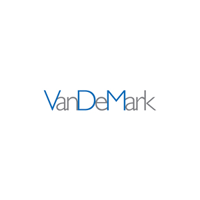
RELATED BLOG POSTS
1 min read
Ingredient Spotlight: Pigment
Vibrant Results Start with Precision Mixing
Start Reading
1 min read
Why Proper Dispersion Matters in Chemical Mixing
In the agrochemical and specialty chemical industries, precision and performance go hand-in-hand. Whether you're manufacturing ...
Start Reading
4 min read
Optimizing Manufacturing with Diamix CX Mixing Technology
Unveiling the Power of Enclosed Mixing Systems In the ever-evolving landscape of manufacturing, the quest for efficiency and ...
Start Reading